人海戦術に代わる担い手として
18人の現場を2人に減らす
───産廃処理工場にロボットを導入された目的を教えてください。
これから人口が減少し、働き手がいなくなるのが分かっていますので、そのために何か手だてはないかと探ったのがきっかけです。解決の一環として結果的にロボットが入りましたが、ロボット以外の選択肢があればそちらでも良かったんですね。
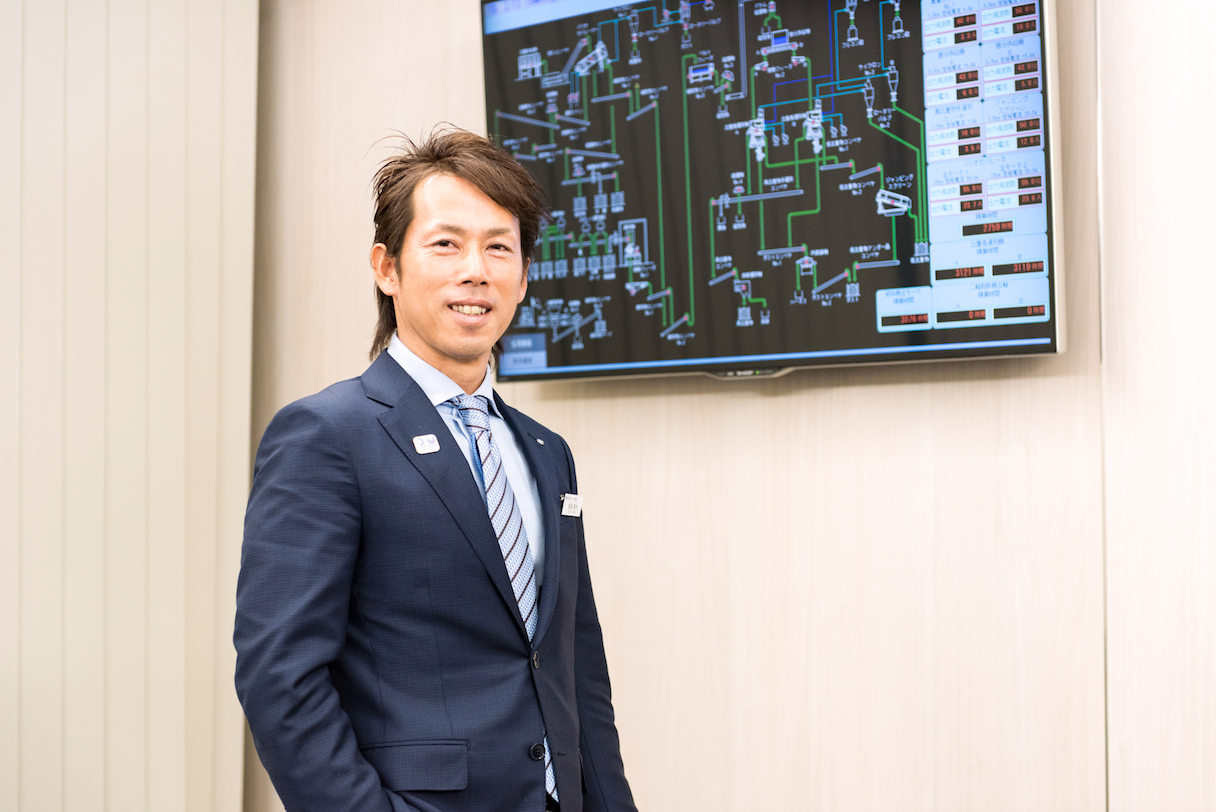
株式会社シタラ興産 設楽竜也 代表取締役社長
ただ、工場をロボット化したことで、これまで18人の社員が立っていた現場を今では2人にまで減らせました。人があまりいなくても工場がきちんと回せるという、産業廃棄物業界ではあまり例のなかった事例だと思います。
───全部で21工程ある混合廃棄物の選別過程のうち、この図では5番の工程にあたる「紙くず、木くず、がれき類、廃プラ、石膏ボード、ガラス・陶器くず」の選別にロボットを導入しているのですね。

混合廃棄物の選別を示した図。24時間で2,000トンの処理能力がある
われわれの業界は、この工程にすごく苦労しています。あとの工程はロボット以外の機械でもやれる可能性がありますが、ここだけは人海戦術に頼るしかありませんでした。
かつて私も携わっていましたが、ゴミが流れてくるコンベアの横に立って、ある人は木を拾い、ある人はがれきを拾って箱に入れる。それを1日やるんですね。まったく楽しくはないです。
仕事とは面白いかどうかでやるものじゃないですが、とてもじゃないけど「やりがい」がありません。よく選別できたと褒めてあげることもできないのです。箱の中を見ても、誰がどれだけ取ったか分かりませんから。
───18人を2人まで減らせたということですが、人はどのような作業を担当しているのでしょうか。
選別行程の最後にチェックの2人だけを残しています。要はスプレー缶や乾電池などの危険物が流れていないかの確認です。その前の工程にマグネットが設置されていますが、くっつかない場合もありますから。
あとは使い捨てカイロも取り除きます。この後の高速のハンマーで叩く工程で一気に発火する可能性があるからです。そういう危ないものが来たら取る。危険物かそうでないか、を素材の情報だけで判断するのは難しいので、ロボットに拾わせるのは難しいです。
機械にとっては過酷な現場
───これまで混合廃棄物の選別が人間でなくてはいけなかったのは、どういった理由だったのですか。
まずは産業廃棄物向けにロボットをつくるメーカーが圧倒的に少ないということがあります。ロボットやAIの技術は、最初にクルマやエレクトロニクスなどの違う業界に行ってしまいます。あとは倉庫業など、単純でやりやすい仕事の置き換えです。機械的動作ができて、ちょっと考えることができればいいというようなものです。
一定の動作でネジを打ち続けるのとは違って、ゴミを見て、判別して、選び取るというのは難しく、社会にとって大事な産業と言ってくださる方は多いのですが、目を向けてくれる会社がとても少ないです。
シタラ興産のプロモーションビデオ。ロボットの映像は54秒から
コンピューターのクリーンルームなどに比べたら過酷な現場です。ゴミの中に機械を配置するので粉じん対策も必要ですし、熱の排出も考えなくてはいけません。
私たちもいざロボット化を考えたとき、選ぶ余地は少なかったですね。世界中でフィンランドのゼンロボティクス社しかつくっていなかったし、それも未完成の製品なんです。機械としてはでき上がっているけれど、AIの部分が発展途上という意味です。
今、ゼンロボティクスのロボットは世界の15カ国で動いています。アジアでは日本、中国。あとは米国やヨーロッパの都市です。
───度々、社長自身も足を運ばれているというゼンロボティクスとはどういう企業なのでしょう。
私も行って驚いたのですが、ほとんどが博士号を持つ30名ほどのプログラマー集団です。もちろん彼らは全体設計をしていますが、機械の製造は下請けの会社に発注するので、頭脳ばかりつくっている会社ですね。
ロボットのメンテナンスなどに関しては、フィンランドのJTA社という会社がやって来ます。彼らは機械はできるけれど、脳は扱えない。だから2社が一緒になって担当する感じです。
───今日お邪魔しているこのサンライズFUKAYA工場ができたのは、いつ頃ですか。
2016年の5月です。そこからラインを全部引き直して、ロボットを導入する工事が始まりました。私と部下の宮下(智則)がいろいろなところを7年間ぐらいかけて回り、どうやって工程を分けているかを見て設計したラインです。
同じ年の11月にフィンランドの工場で使っていたデータをうちの方に送ってもらい、AIのトレーニングを開始しました。ただ、始めてみたら実際のゴミが全然違うので、まるで取れないんですね。向こうでは大きな木やブロックなどを選別することが多いようです。
そこから日本独自のゴミについてうちの会社で教えながら、機械学習に取り組んでいきました。
ソフトとハード、両方の開発に協力
小さくて難しい日本のゴミ選別
───日本の廃棄物が海外と違うのは、どういうところなのでしょう。
まず、廃棄物のサイズがとても小さいです。建築リサイクル法(※1)が前提にありますので、みんな仕分けてしまう。大手ゼネコンの方から聞いた話ですが、95%ぐらいまでは仕分けられている。ただ残りは、どうしても現場で分けられないゴミが出てくると。
この5%ばかりを集める工場があってもいいじゃないかというコンセプトでラインの設計は始まりました。つまり、ターゲット顧客は同業者だったんですね。
だから、私たちが扱う廃棄物はゼンロボティクスの中では一番小さくて難しい。「これができるようになったら、きっとこのロボットは完璧になるよ」と話していて、大きいゴミから小さいゴミまでカバーできるよう、他の国のロボットと連携してプログラムのアップデートを繰り返している途中です。
───共同開発をしているイメージでしょうか。
小さなゴミをつかめるように、協力している関係です。ゼンロボティクスからはソフトウェア以外にも「次はこういう爪を持ってくるから、試験的に使ってみてくれないか?」「こういう強度を足したものをつくったので、これを試してほしい」といったリクエストを受けることがあります。
───普段はここで撮影した画像や動画をフィンランドに送り、そこで共通データみたいなものをつくるのですか。
カメラがすべてのロボットに付いていて、取れているか、取れていないかをリアルタイムで全部認識しています。インターネット経由でカメラをずっと繋いでいるので、世界中どこからでも常時監視が可能です。
───実際に見ていると、先ほどからロボットの腕が大きなゴミをつかみにいくのが確認できます。
それ以外のゴミは、あえてロボットを動かさなくてもいい細かさなんですね。このサイズでつかんでしまうと、一緒に別のものまでつかんでしまう。それを「つかみにいくな」とインプットしているのです。
ある一定の大きさを超えたゴミに対してのみ動くというセッティングをしていますが、いつでも設定の変更は可能です。
週に1度、復習の時間を設ける
───どの段階でゴミを識別しているんでしょうか。
近赤外線金属センサー、3Dレーザースキャナー、ハイパースペクトルカメラなどを使って画像認識しています。ゴミがカメラの下を通った瞬間に撮影して、1回あたり200個くらいを識別しているということです。そうして何が最適に取りに行けるかを判断し、その後で腕を動かすわけですね。
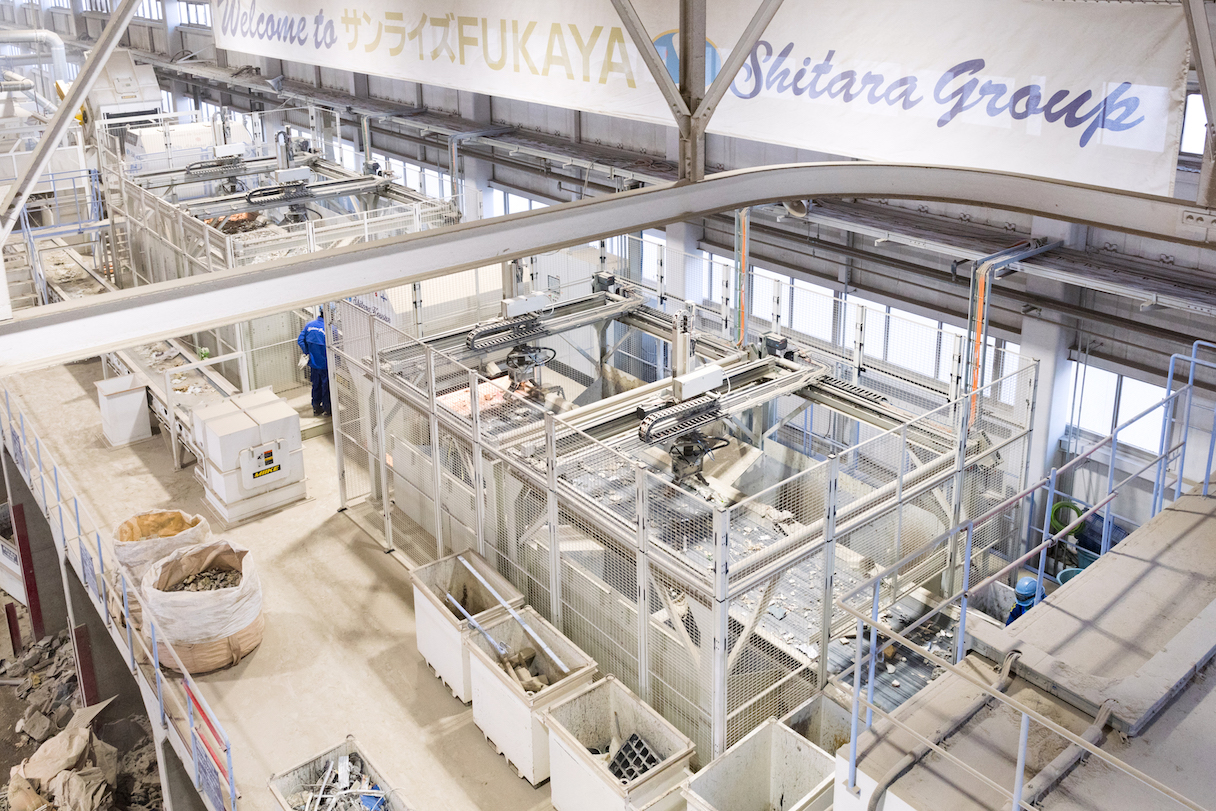
シタラ興産はゼンロボティクスのロボットを2台導入。2つのカメラと4本のグリッパー(腕)がリサイクルできるゴミを逃さない。写真の左から右へコンベが流れている。人間が2人体制で残りのゴミに紛れた危険物のチェックを行った後、ハンマー破砕機にかけられる
───ゴミには硬いもの、柔らかいもの、いろいろありますが、そのあたりはどう対応しているのですか。
導入当初、AIが調整したコンプレッサーの力でつかみにいったときは、強くつかみすぎて塩ビパイプなどが割れてしまいました。それではいけないとうちのメカニックがエアの調整をして、動作スピードは変えずに、つかむ力をソフトにしていったんですね。
また、そんなにガチンとぶつかってから取る必要はないので、プログラム上でも「表面から取る」という方式に変えました。1年ぶりに見学に来ていただいたお客様は「だいぶ取り方がソフトになったじゃないか」とすぐ分かったようです。
───運用面で難しいところはあるでしょうか。
アップデートが成功ばかりとは限らないことです。より細かいものをつかめるようにアップデートを重ねるんですが、先日は金属をがれきだと反応するようになってしまい、そのアップデートをキャンセルしました。
───間違った学習を積んでしまったんですね。
そうです。うちで学習させた結果をフィンランドに送るんですね。それを彼らがプログラムとして固めるわけです。その結果が返ってきて、データを1日かけてインプットします。
さて、アップデートの結果はどうだろう? と見たら、金属とがれきを間違ってつかむようになっている。そうなったら前の段階に戻して、どこが悪かったかを検証する。その結果、グレーの金属とがれきが似ていたのが理由だと分かりました。
機械学習をやってみて実感したのは、本当に「刷り込んでいく」という、まるで書き取り練習のような積み重ねだということ。ダメだったもの、間違ってしまった結果も取っておいて「これとこれは間違っていたから取っちゃダメだよ」と学習させていくんですね。
───まるで、子どもに何かを教えるようなものですね(笑)
本当に子どもに対するように教えます。それを繰り返し、繰り返しやることにより、データがある程度でき上がってきます。それをゼンロボティクス側に1回渡す。アップデートのデータを戻してもらって「さぁ、上達したかな?」という感じです。
普段の動きは決められたプログラム通りに行っているので変化はありません。ただ、毎週土曜日にはトレーニングをする「勉強の時間」を決めています。3カ月ぐらいの単位で「取ってはいけなかったもの」をリスト化し、繰り返し刷り込みます。そういったデータを向こうに送ってアップデートに役立てるのです。
リサイクルから焼却まで取り組みたい
10年先を見据えた先行投資
───大型の投資で最先端の機械を導入した場合、ソフトウェアは随時アップデートできたとしても、ハードやシステムが古くなってしまうのではないかという懸念はあったかと思うのですが、心配はありませんでしたか。
日常的に使っている以上、機械の劣化は仕方がないと思います。最先端のロボットを導入した理由は、10年経ったときに、まだ現役でいられるシステムづくりが大事だと考えたからです。そのとき時代が先行していてもいいんですが、ある程度はまだ役立つ工場でないといけません。
私たちのような中小企業は、何回も手直しする資金はありません。だから1回の投資で、なるべく10年は先を見なくてはいけない。10年後に周りと同水準を保っていないと、またつくれるチャンスは来ないかもしれないから、相当考えて未来を見ます。
───このシステムに関する今後の課題や要望を聞かせてください。
機械はとりあえず完成しているし、プログラムもどんどん完成形に近付けてはいます。でも100点ではないので、ずっと練習させ続けるかもしれません。メカニックたちの目標も高いところにあって、今は5cmの高さのゴミを拾えるのですが、さらに小さなゴミにも挑もうとしています。
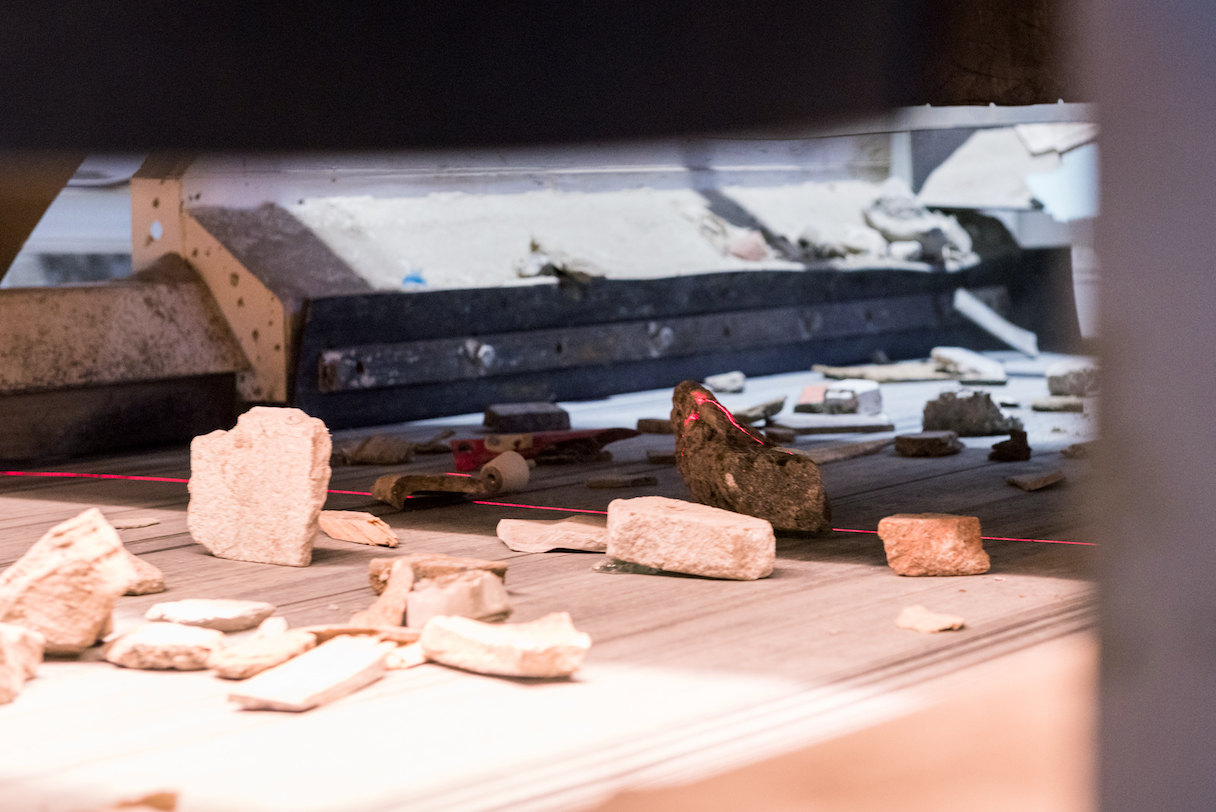
コンベアから流れてくる廃棄物の形状を、大きさや色、高さなどで識別。機械学習で素材を推定し、それに応じたアームが後からつかみにいく
その次にうちがやりたいことは、RPF(Refuse Paper & Plastic Fuel)(※1)製造の24時間化です。今もRPFはつくっていますが、文字通り24時間止まることなく、廃プラスチックから固形燃料のRPFをつくり続けるためです。
この工程を拡張するための工事は申請済みですが、許可が下りるまでには3年くらいかかるので、3年半後には着工したいと考えています。
さらに4年後、最終的には「焼却」まで取り組みたいです。リサイクルと焼却というのは、イメージが逆じゃないですか。ただ、燃やさなくてはいけないゴミというのはどうしても出るんですね。
今の焼却炉は昔より全然ダイオキシンが出ません。むしろ熱から発電ができるし、お風呂を沸かしたりもできて、いろんな機能を兼ね備えている。ゴミを埋め立てるのではなく、まず焼却する。そこから出た灰も、今ではリサイクルができます。
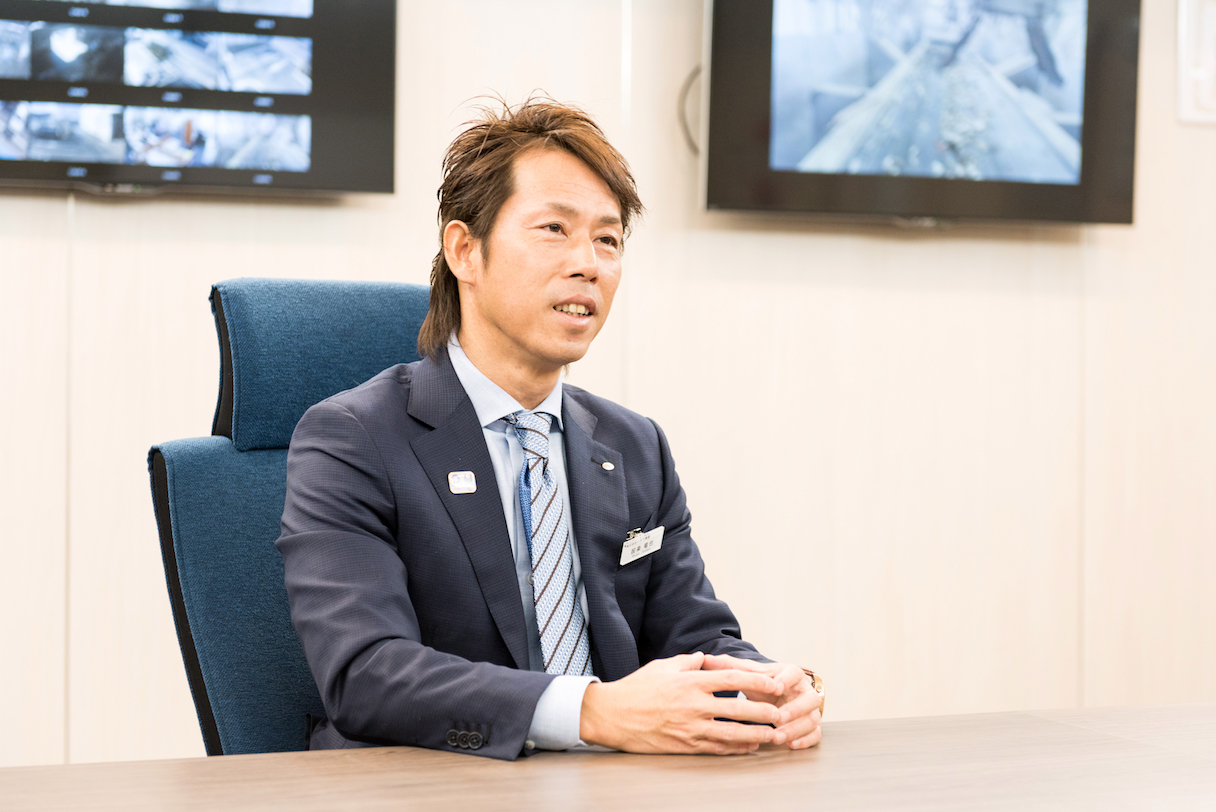
かつてはホテルマンを目指していたという設楽社長は、シタラ興産の2代目。次の代に向けた青写真も明確に描いている
そうした焼却炉の中に、またAIを入れたいです。例えば、夜中などに軽いエラーが起きたとします。そのとき、今までの蓄積したデータから良いプログラムが入っていれば、最善な対処策が実行される。そうすると監視員が要らなくなるんです。
次は機械を買うというより、AIだけを買うようなことを考えています。焼却炉にも使えるようなのであれば、違うところでも使えると思います。
社会に溶けこめる仕事として
───最後にシタラ興産が目指すゴールについて伺います。どこを想定していますか。
2025年には人が少なくなってくる。若い子も減ってくるので、うちの社員も若手でも30代後半になってくる可能性があるんですね。そこからRPF工場で働いたり、焼却炉の仕事を覚えたりして、10年も働いたら体がそろそろおじさんになっているでしょう(笑)
いろいろ働いてきて、いい知恵を持っている人間が、そのとき作業員のままではもったいないんですね。まして人が少ないから、後輩が入ってくるかどうかも分らない時代になります。だからAIの判断によって機械を動かしたり、たとえ素人がやっても同じように機械を動かせる工場が私の理想です。
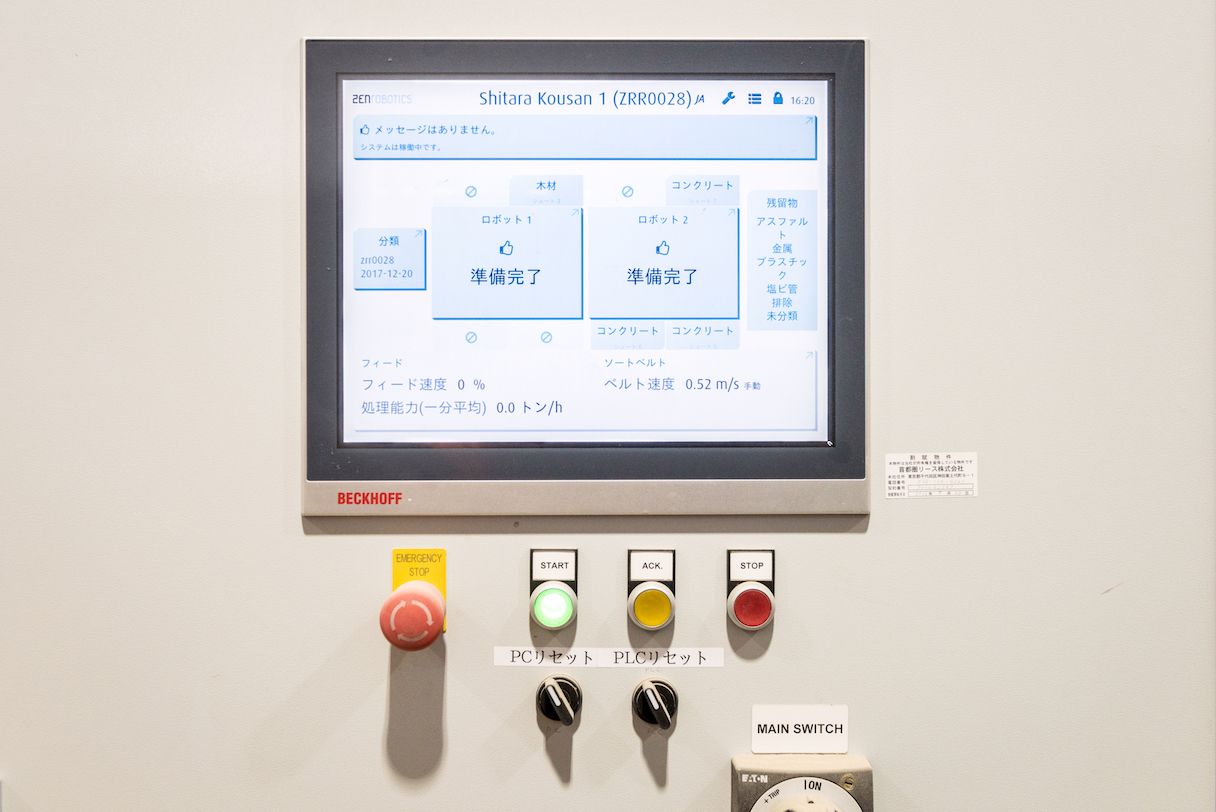
ロボットの操作盤は日本語に対応。作業員はこのタッチパネルを使って、選別する廃棄物をアームごとに設定する。素材名がボタンで画面表示されるので、簡単に操作できる
そして、これは言い過ぎかもしれませんが、産業廃棄物処理がやはり大事だということを皆さんに認識してもらうのがゴールでしょうか。リサイクルも大切なのですが、まずはゴミを処理しない限りリサイクルもできないですから。
まだまだ産廃処理屋さんは嫌われているという現状がありますので、社会に愛されるまではいかないとしても、社会に溶け込める仕事にしたい。これが私たちの最終的な目標であり、夢なんです。
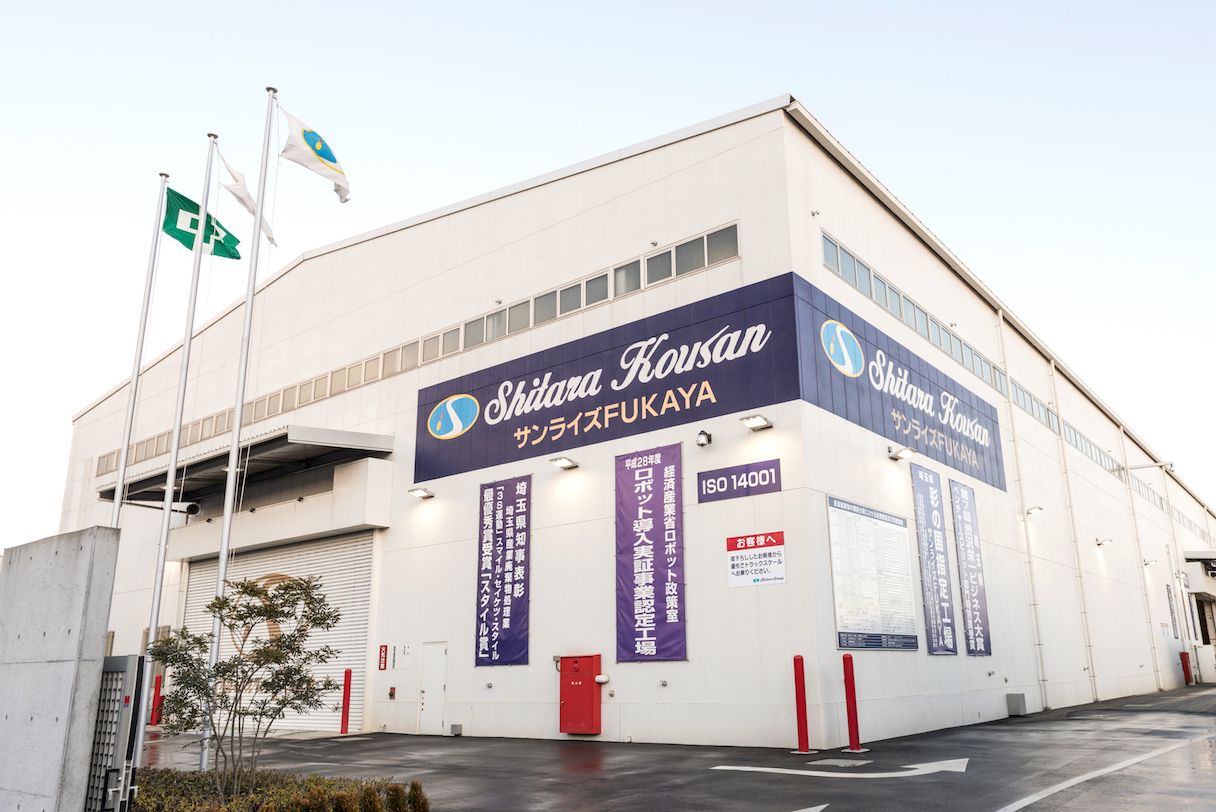
シタラ興産の「サンライズFUKAYA工場」は、平成28年度 経済産業省ロボット政策室「ロボット導入実証事業認定工場」に認定されている
素材としてのリサイクルが難しい古紙やプラスチックゴミなどの廃棄物を主原料とした固形燃料。